آلکیل آمونیوم کلراید که در آن R زنجیره هیدروکربن بوده و نمایانگر فعال کننده سطحی می باشد. زنجیره جزء آب گرا یا چربی گرا مولکول است. گروه NHCI جزء آب گرا می باشد. در فاز آبی مولکول صابون یونیزه شده و کاتیون های آلکیل آمونیوم و کلرید را تولید می کند.
هنگامی که امولسیون ساخته می شود کاتیون ها توسط ذرات کروی قیر جذب شده و جز، چربی گرای R جدا می شود. گروه آمونیوم نیز در وجه مشتر آب قیر جایگزین می شود. آنیون های CL نیز در آب باقی می مانند.
گلبول های قیر به علت وجود گروه آمونیوم دارای بار مثبت هستند. این گروه ها اطراف ذرات قیر را احاطه می کنند. از یک طرف این بار مثبت باعث پایداری مولکول در اثر وجود دافعه الکترواستاتیک شده و از طرف دیگر موجب چسبندگی ذرات قیر به سطح ذرات مصالح سنگی دارای بار منفی می شود.
مصارف متعددی برای امولسیون های کاتیونی وجود داشته و لذا تکنیک های مصرف مختلف و فرمولاسیون های مختلفی برای آنها ارائه شده است، نیازی به نام بردن از همه این فرمول ها نبوده و تنها به چند نمونه از معروفترین آنها بسنده میشود.
پر مصرف ترین گروه مواد فوق امولسیون های زودشکن (گروه ECR) می باشد امولسیون های قیری و امولسیون های قیری اصلاح شده با پلیمر برای اجرای آسفالت سطحی کاربرد وسیعی دارند.
پرمصرف ترین فعال کننده های سطحی شامل آلکیل آمین ها، آلکیل آمیدها و آمیدازولین های نیتروژن دار می باشند. این مولکول ها باید به صورت نمک باشند. البته امکان استفاده از اسیدهای آلی مانند اسید استیک، اسید فرمیک و غیره نیز وجود دارد. در عمل تنها از اسید کلریدریک استفاده می شود زیرا محدودیت های کمتری در رابطه با مصرف آن وجود دارد. مثالی از یک فرمولاسیون امولسیون گروه 65ECR برای یک قشر آسفالت سطحی دو لایه به صورت ذیل می باشد:
• چربی آلکیل تری متیلن دی آمین 1.5 تا 2.2 کیلوگرم
• اسید کلریدریک ۳۲٪ 1.5 تا ۲ کیلوگرم
مثالی از فرمولاسیون امولسیون گروه 69 ECR برای آسفالت سطحی یک لایه نیز به شرح زیر می باشد:
• ترکیب آلکیل آمید و آلکیل آمیدو آمین 2 تا 2.5 کیلوگرم
• اسید کلریدریک ۳۲٪ 2.2 تا 2.5 کیلوگرم
مثالی از فرمولاسیون بکار گرفته شده برای گروه امولسیون 60ECR برای ترمیمات جزیی به صورت زیر می باشد:
• آليكل آمیدو پلی آمین 1.8 تا 2.2 کیلوگرم
• اسید کلریدریک ۳۲٪ 7.1 تا 1.2 کیلوگرم
امولسیون های قیری استفاده شده جهت تزریق و یا پوشش مصالح سنگی فاقد ذرات ریزدانه معمولاً از نوع کندشکن (گروه ECM) می باشند. دو مثال مرسوم از این گروه در زیر آورده شده است.
• چربی پلی اکسی پروپیل دیامین پروپیلن ۲ تا 2.5 کیلوگرم
• اسید کلریدریک ۳۲٪ 1.3 تا 2.2کیلوگرم
مثالی از فرمولاسیون برای گروه امولسيون 69ECM جهت ساخت مخلوط های سرد سیلسی d/D قابل انبار به شرح زیر میباشد:
• ترکیب آلکیل آمیدو آمینو الكيل تری متیلندیامین ۳ تا ۴ کیلوگرم
• اسید کلریدریک ۳۲٪ 1.5 تا ۲ کیلوگرم
امولسیون های نیمه پایدار (گروه ECR) معمولاً در کارخانه های آسفالت یا کارگاه توسط تجهیزات مناسب ساخت مخلوط ها بکار گرفته می شوند. این امولسیون ها در ساخت مخلوط های سرد O/D آماده مصرف و نیز مخلوط های گریو امولسیون مورد استفاده قرار می گیرند.
مثالی از فرمولاسیون این نوع امولسیون های گروه 60ECL در زیر آورده شده است.
• ترکیب پلی آمین پلی پروپلین اولئواستریل و چربی دیامین آلکیل تری متیلن ۵ تا ۸ کیلوگرم
• اسید کلریدریک ۳۲٪ ۴ تا ۱۰ کیلوگرم
• همانند آنچه در مورد امولسیون ها آنیونی ذکر شد استاندارد فرانسه امکان ساخت امولسیون های کاتیونی با پایداری زیاد (گروه ECS) را نیز مد نظر قرار داده است. این امولسیون ها به صورت اخص در ساخت مخلوط های سرد به کار گرفته می شوند. یک نوع پرمصرف از این گروه دوغاب آب بندی می باشد.
مثالی از فرمولاسیون یک امولاسیون گروه 60ECS برای مصارف دوغاب آب بندی به شرح ذیل می باشد:
• دی آمونیوم پنتا میتل استریل کلراید ۶ تا 7.5کیلوگرم
• کلرید کلسیم یک کیلوگرم
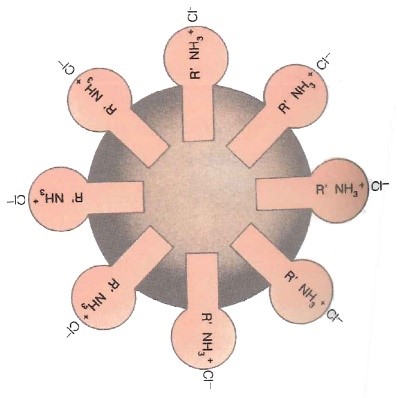
امولسیون های کاتیونی
فاز هیدروکربن پراکنده
استاندارد 000- 65 T شیمیدانان را در انتخاب فرمولاسیون با توجه به امولسیون قیری آزاد گذاشته است. قیر خالص، قیر محلول یا قیر اصلاح شده هر یک با فرمولاسیون خاصی از امولسیون ها ارائه می شوند. علت استفاده از مواد اصلاح کننده قیر، تصحیح امولسیون بوده به نحوی که ترکیب حاصله با ملزومات فنی، محدودیت های ترافیکی و شرایط اقلیمی تطابق داشته باشد.
آزمایش کامل همه ساختارهای ممکن بسیار وقت گیر بوده و لذا تنها ملاحظات کلی که شیمیدانان را در انتخاب ترکیب پایه راهنمای می کند، باید مدنظر قرار گیرند.
توجه خاصی به امولسیون های مورد مصرف در ساخت مخلوط های قابل انبار کردن بایستی معطوف گردد.
انبار کردن این مخلوط ها به مدت چند هفته قبل از مصرف در صورتی امکان پذیر است که انتخاب قير و حلال با دقت صورت گرفته و خصوصیات این مواد عملکردهای مورد نیاز را تامین نماید. حلال مورد مصرف می تواند حلال صنعتی و یا حلال قطرانی باشد. دو ضابطه زیر به عنوان اصول پایه این مبحث بایستی مد نظر قرار گیرند:
• حداکثر میزان کندروانی قیر پسماند که بالاتر از آن پخش و پخش دستی مخلوط را با مشکل مواجه می سازد معادل 0.6 تا 0.8 m2/s (یعنی ۱۵۰۰ تا ۲۰۰۰ ثانیه S.T.V برای روزنه ۱۰ میلیمتری) می باشد.
• حداقل میزان کندروانی قیر پسماند که پائین تر از آن موجب نقصان در چسبندگی مخلوط خصوصاً در راه های با سرعت تردد زیاد می گردد 0.02 تا 0.04 m2/s میباشد (یعنی ۵۰ تا 100 ثانیه S.T.V برای روزنه 15 میلیمتری).
بر مبنای اصول فوق مقدار ایده آل کندروانی قیر پسماند محدوده بین دو مقدار فوق بوده که بر اساس دمای محیط پخش مخلوط محاسبه می گردد.
توجه خاصی به امولسیون های مورد مصرف در آسفالت های سطحی باید معطوف گردد. این امولسیون ها باید از چسبندگی و پیوستگی مناسبی در قیر پایه برخوردار باشند. مصالح سنگی موجود در سطح این رویه های محافظ در اثر نیروهای برشی بزرگی قرار می گیرند. ملزومات ذیل بایستی به صورت همزمان برای تحمل این نیروها توسط ذرات مصالح سنگی واقع در سطح تامین شوند:
• ذرات سنگی سطحی نباید از قير جدا بوده و قیر نیز بایستی به سطح زیرین کاملاً متصل باشد.
• قیر تحت اثر این نیروی کششی نباید دچار گسیختگی برشی شود.
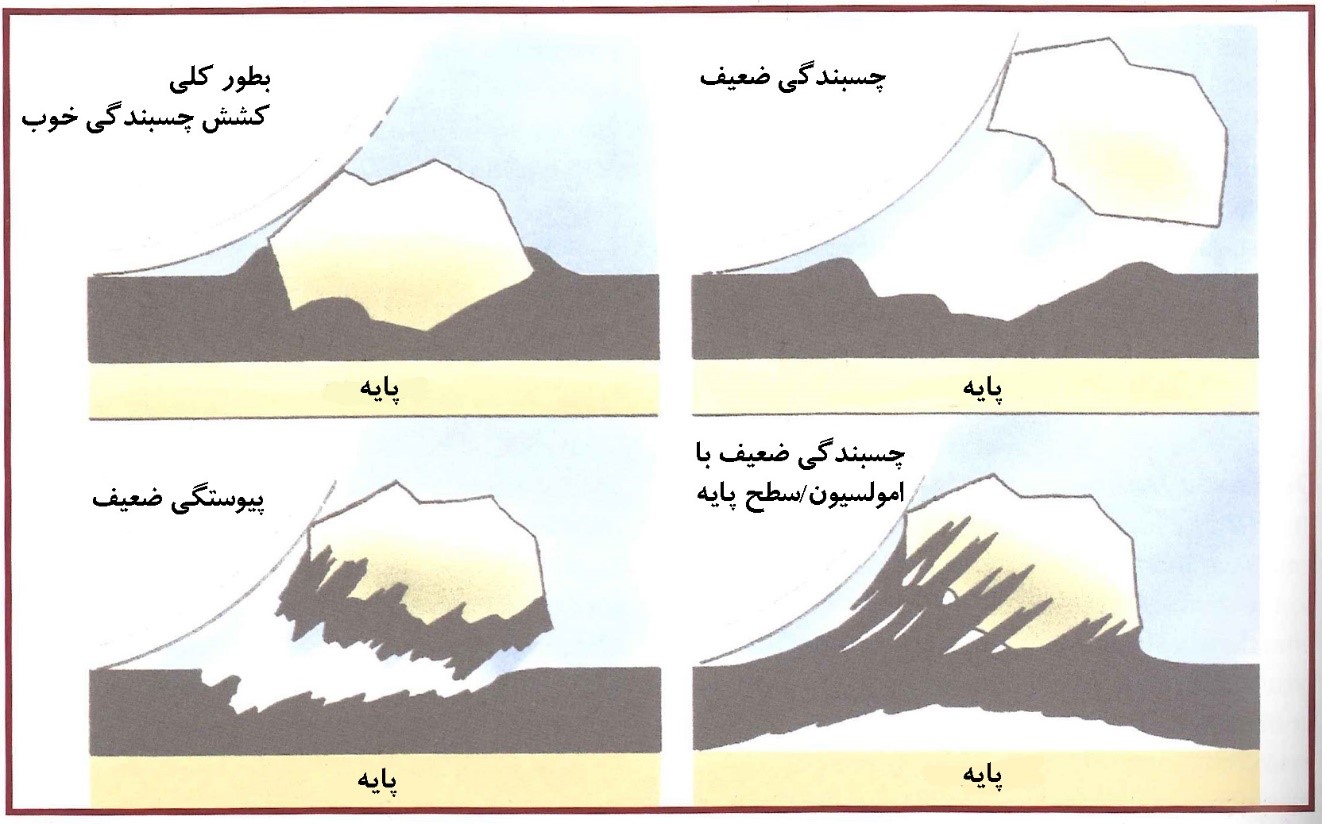
تنها در صورتی که شرایط ذیل محقق گردد چسبندگی و یا اصطلاحاً «ظرفیت چسبندگی» کافی موجود خواهد بود.
- اولاً ضروری است که قیر با مصالح موجود در آن و خصوصاً ذرات موجود در سطح رویه کاملاً در تماس باشد. برای این مقصود نه تنها بایستی قیر به صورت سیال باشد بلکه حتی بایستی از رطوبت کافی نیز برخوردار بوده که این مسئله در مورد امولسیون های کاتیونی نسبت به امولسیون های آنیونی، با مشکل بیشتری مواجه می باشد. در مورد اصل اول یعنی سیال بودن قیر به اندازه کافی، معمولاً مشکلی وجود ندارد مگر آن که شرایط غیر منتظره ای مثل وجود نمک در امولسیون به وقوع پیوندد. شرط اول چسبندگی اصطلاحاً «چسبندگی فعال» نامیده میشود.
- سپس در صورتی که شرط اول محقق شود امولسیون قیری و مصالح سنگی بایستی توسط عامل جدا کننده آب از هم جدا شوند. این مسئله معمولاً در حضور ذرات ریز دانه مصالح سنگی مانند فیلر و تحت شرایط ترافیکی سنگین دیده میشود. شرط دوم چسبندگی اصطلاحا «چسبندگی مقاوم» نامیده میشود.
پیوستگی
این بحث با عنوان «پیوستگی داخلی قیر» و یا مقاومت برشی قیر نیز مطرح می شود. این پیوستگی به چند عامل بستگی داشته که مهترین آن کندروانی میباشد. پیوستگی، وابستگی زیادی به کندروانی داشته و این پارامتر نیز به نوبه خود از دمای محیط تأثیر می پذیرد. بر همین اساس در یک دمای پایین مشخص چسبانده قیری تحت اثر نیروهای مکانیکی بسیار شکننده می باشد. از طرف دیگر در صورتی که دما از میزان معینی تجاوز کند قیر به صورت سیال در آمده و از مقاومت کافی برای تحمل نیروهای کششی برخوردار نخواهد بود.
با توجه به گفته فوق چگونه می توان مخلوط های ساخته شده از امولسیون های کاتیونی را پخش کرد؟
این چسباننده ها بر خلاف امولسیون های آنیونی از رطوبت کمتری برخوردار می باشند زیرا عوامل فعال کننده سطحی در آنها رفتار آب گرای کمتری دارند. از طرف دیگر آنها چسبندگی مقاوم بیشتری را به چسباننده قیری می بخشند. در تئوری راه حل ساده ای وجود دارد، برای بهبود خصوصیات رطوبتی می توان بر سیالیت قیر پایه افزود. البته در این صورت پیوستگی در دمای بالا کاهش یافته و چسباننده نرمی حاصل می گردد. این مسئله یکی از تناقضاتی است که محققین بایستی به آن توجه بیشتری داشته باشند.
بر اساس مطالب فوق یک حلال، یک پلیمر یا هر دوی آنها برای تأمین الزامات پیوستگی به قیر پایه امولسیون اضافه می شوند. برای جمع بندی می توان گفت که در فرمولاسیون امولسیون های کاتیونی مخصوص لایه های رویه باید از بهترین انتخاب برای فعال کننده های سطحی استفاده کرد به نحوی که از نقطه نظر شیمیای چسبندگی بلند مدت امولسیون به سطح زیرین و مصالح سنگی و همچنین ایجاد تعادل در ترکیب چسباننده اطمینان حاصل گردد. این تعادل بایستی بین عواملی از جمله نیازهای مطلوب بلافاصله پس از شکست امولسیون، سیالیت کافی چسباننده جهت پوشاندن مصالح سنگی وسفت بودن چسباننده به نحوی که قادر به تحمل تنش های اعمال شده توسط ترافیک باشد برقرار شود.
ایجاد تعادل بین عوامل فوق با توجه به این نکته انجام می گیرد که رفتار امولسیون بستگی زیادی به نوسانات دمای محیط خواهد داشت. حال باید به بحث در مورد کیفیت قیر پایه امولسیون برای مصرف در مخلوط های مختلف پرداخته شود. این مصارف مخلوط ها، اسلاری سیل ها، مخلوط های گریو امولسیون و غیره را در بر می گیرند. در این مورد قير نباید توسط حلال آن قدر رقیق شود که خصوصیات آن دچار نقصان گردد. البته جهت رفع مشکلات مربوط به حلالیت میتوان پلیمر به قیر پایه اضافه نمود. این پلیمرها می توانند به صورت لاتکس و یا مخلوط در قیر پایه مورد استفاده قرار گیرند.
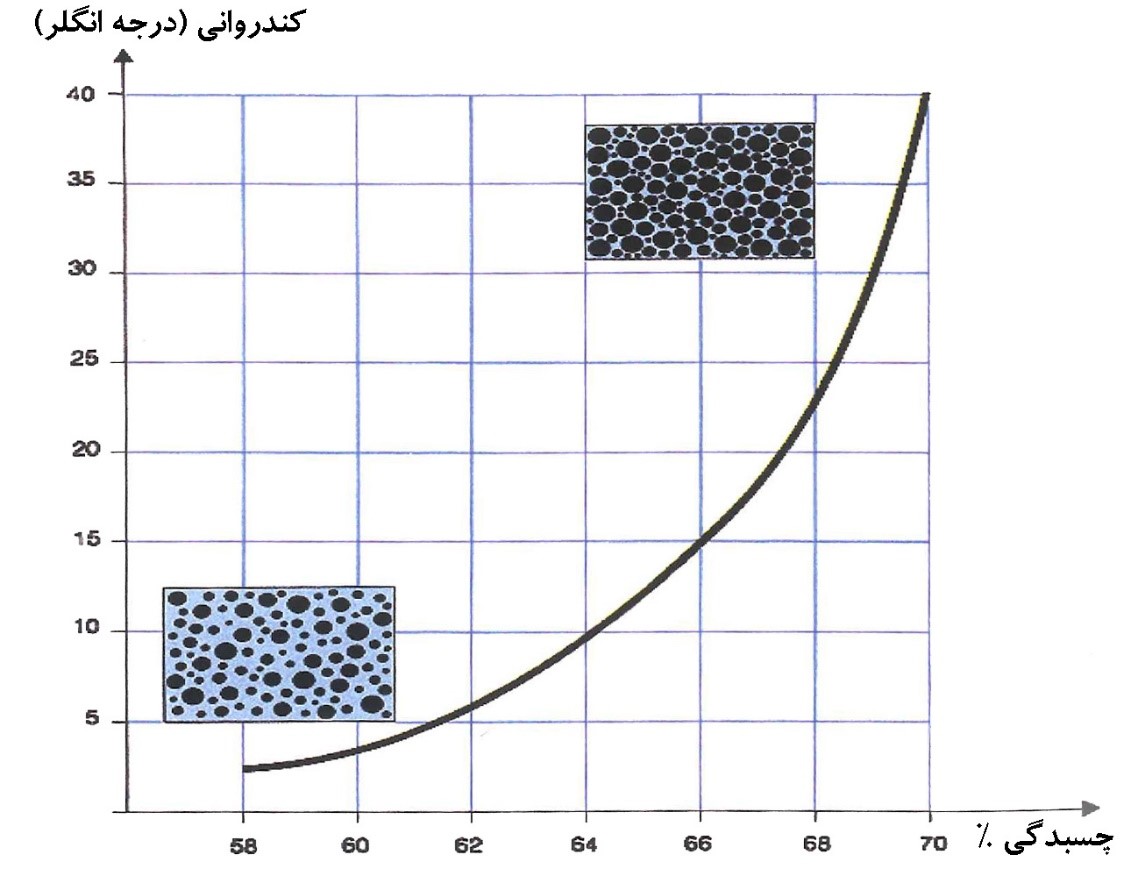
کند روانی امولسیون به صورت تابعی از مقدار قیر پایه
خواص
مشخصات امولسیون قیری را می توان به دو گروه تفکیک نمود:
خواص ذاتی
این مشخصه ها شامل پارامترهایی هستند که به تولیدات معدنی مصرف شده همراه امولسیون ارتباطی ندارند. این مشخصهها کندروانی و پایداری در انبار را شامل می شوند.
خواص خارجی
این خصوصیات شامل پارامترهایی هستند که به رفتار امولسیون در مصارف مختلف مربوط می شوند که از آن جمله می توان به چسبندگی و سرعت شکست اشاره کرد.
کندروانی
عامل اصلی موثر در کندروانی امولسیون غلظت فاز پراکنده می باشد. برخی محققین معادله ای را برای نمایش رابطه بین کند روانی و غلظت فاز پراکنده ارائه نموده اند. برخی از این فرمولها را میتوان در مقاله نوشته شده توسط G.Romand تحت عنوان امولسیون های قیری در مجله LCPCدر ژوئن 1974 مشاهده کرد.
سایر عوامل موثر بر خصوصیات رئولوژیک امولسیون عبارتند از:
- نوع فاز پراکنده منشأ قیر
- وجود رقیق کننده (نفت یا روغن روانساز)
- نوع و مقدار فعال کننده های سطحی
- فرآیند ساخت (نوع آسیاب)
پایداری در انبار
امولسیون های قیری تحت قوانینی مشابه سایر امولسیون ها قرار دارند. بر همین اساس آنها از نظر ترمودینامیکی سیالاتی پراکنده و ناپایدار هستند. این ناپایداری از تمایل سیستم به کاهش انرژی آزاد سطحی با گذشت زمان ناشی شده که در عمل از آن تحت عنوان کاهش تدریجی سطح مشترک قیر - صابون نام برده می شود. نتیجه نهایی این فرآیند تفکیک اجزاء به دو فاز مخلوط نشدنی می باشد.
- اولین نشانه تفکیک امولسیون پدیده شکست بوده که به نشست فاز پراکنده در قسمت پائینی و گاهی در قسمت بالا منجر می شود. تفاوت چگالی دو فاز نقش اساسی را در این پدیده بر عهده داشته و سرعت آن توسط قانون استوکس تعیین می شود.
- مرحله بعدی تجمع می باشد، این مرحله یک حالت معکوس بوده که در آن هر ذره کوچک کروی هنوز هم توسط یک لایه نازک از فعال کننده سطحی محافظت می شود.
- مرحله آخر جوش خوردگی (انعقاد) می باشد. ذرات کروی در اثر گسستن لایه محافظ فعال کننده سطحی به هم متصل می شوند. این فرآیند غیر قابل بازگشت بوده و پیشرفت آن مشابه همگرفت محلول های کلوئیدی می باشد.
عاملی که میزان پایداری امولسیون در انبار را تعیین می کند اندازه ذرات بوده که به نوبه خود به پارامترهای مختلفی از جمله نوع و مقدار امولسیون ساز، سرعت خنثی سازی (PH فاز آبی)، منشأ و گروه قیر پایه، دمای فازها به ویژه دمای قیر، عمر امولسیون و نوع آسیاب امولسیون بستگی خواهد داشت.
سرعت شکست و پتانسیل زتا
پایداری امولسیون های قیری در تقابل با مصالح سنگی یک خصوصیت پایه به شمار می رود که موضوع مقالات بسیاری در این زمینه نیز بوده است. از آن جمله می توان به مقالات ارائه شده توسط J.Bellenger در ۱۹۵۳، J.C.Vogt در ۱۹۶۴، M.Bourell و C.Chamber در ۱۹۸۷ اشاره کرد. این مسئله همچنین منجر به پیدایش تئوری های علمی مختلفی در مورد مکانسیم شکست امولسیون گردید. روش های متعددی نیز جهت عددی سازی این پارامترها ارائه شد. روش های آزمایشگاهی توسط U.Isacsson بنا نهاده شد. این نویسنده ۳۸ روش مختلف برای این کار ارائه نموده است. قطعاً روش های دیگری خارج از لیست این نویسنده نیز وجود خواهد داشت. این مسئله نشانگر پیچیدگی این مشخصه بوده که مارا مجاب می سازد در تحقیقات آتی به آن بیشتر بپردازیم. بدون ورود به جزئیات، یادآوری مفاهیم پایه مهم به نظر می رسد.
شکست
فرآیندی است که در آن مراحل زیر به صورت متوالی بوقوع می پیوندند:
- تفکیک، که به نشست یا تشکیل کرم منجر می گردد.
- تجمع، که در اثر نزدیک شدن گلبول های فاز پراکنده و تشکیل یک شبکه باز بوقوع می پیوندد.
- انعقاد که به معنای تشکیل یک توده متراکم و جدا شدن آن از سایر محلول میباشد.
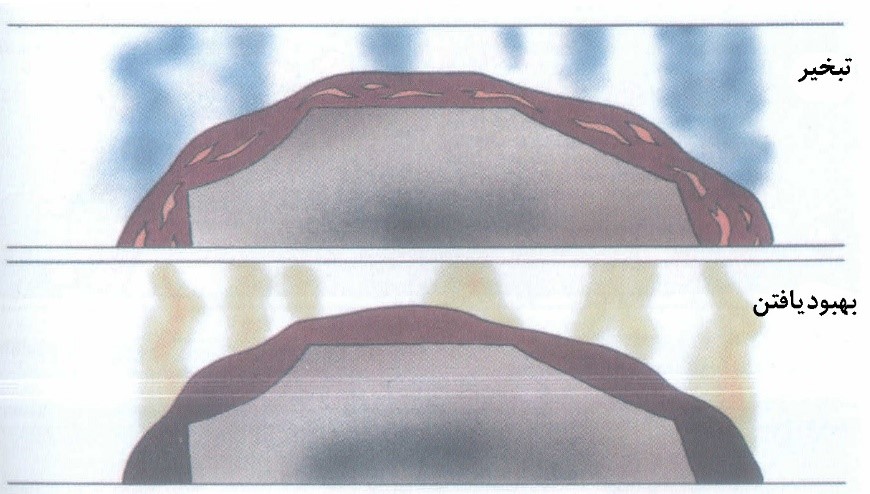
شکست
در مجموعه اسناد منتشر شده توسط G.G.Ramond ,A.M,Ajour ,R.sauterey یک بازبینی تئوریک و عملی از چسبندگی به عمل آمده که با توجه به امولسیون های قیری، چسبندگی بین امولسیون و مصالح سنگی به صورت شماتیک ذیل بیان می گردد.
در حضور مصالح مثبت از نظر الکترو استاتیکی (مانند کلسیم و بازالت):
• اندر کنش بین مصالح آهکی و اسیدها، فرمولاسیون با استفاده از کربنات آمین غیر محلول برای امولسیون های کاتیونی مورد استفاده قرار می گیرد.
• جاذبه بین گلبول های قیر دارای بار منفی و تشکیل صابون غير محلول کلسیم برای امولسیون های آنیونی.
در حضور مصالح منفی از نظر الکترواستاتیکی (سیلکس، کوارتز، گرانیت و پورفیری):
• جاذبه گلبول های قیر دارای بار مثبت و تشکیل سیلیکات آمین غیر محلول برای امولسیون های آنیونی
• هیچ اندر کنشی برای امولسیون های آنیونی وجود نداشته و در این حالت چسبندگی وجود نخواهد داشت.
در واقع اکثر مصالح سنگی مورد استفاده در فعالیتهای راهسازی در کشور فرانسه به همراه امولسیون های کاتیونی در ساخت مخلوطها بکار گرفته میشوند.
نتیجه گیری
امولسیون قیری یک چسباننده پیچیده می باشد. علت این امر تنوع فرمولاسیون و وابستگی زیاد مشخصات آن به قیر پایه مصرف شده در امولسیون است. بدیهی است که هنوز نیاز به انجام مطالعات بسیاری راجع به این چسباننده ها وجود داشته و بایستی روش های فنی اقتصادی تر از نقطه نظر مصرف انرژی و آلودگی های زیست محیطی مورد بررسی قرار گیرند تا مصرف امولسیون ها در تکنیکهای راهسازی از رواج بیشتری برخوردار گردد.
امولسیون تهیه شده متشکل از از دو فاز پیوسته شامل آب و ماده امولسیون ساز و ناپیوسته شامل قیر می باشد. در امولسیون های قیری، قیر با مقدار بسیار کم مواد امولسیون ساز به صورت دانه های بسیار ریزی در آب پخش می شود و پس از پخش شدن روی مصالح سنگی شکست قیر اتفاق می افتد و قیر خالص باقی می ماند.